The foundation of all digital manufacturing systems is data. When we think about manufacturing data, it is helpful to segregate data into two types 鈥 measured data and processed data. These two types of data originate from different sources, and each should be handled somewhat differently. Measured data originates from electronic controllers and sensors on the shop floor. This type of data provides a "true representation" of the status of what is happening in your shop operations. That is, assuming the data is not corrupted and is measured/collected properly. Processed data, on the other hand, is typically not generated directly on the shop floor but is the result of calculations or other manipulations to create a higher level of extraction of information.
Multiple types of data can be collected directly from shop operations:
Continuous variables 鈥 Results of measurements of analog process variables (temperatures, pressures, currents, etc.) or accumulators like timers and counters.
State 鈥 Values indicating the current state of a multistate data type (on/off, open/closed, etc.).
Modal 鈥 Indication representing the operating mode of a function (auto, manual, semi-automatic, running, stopped, etc.).
Alarm status indicates the presence or absence of alarms or warning conditions.
Measured data can generally be considered valid data. It has not been manipulated or combined with other information to create value. However, valid data does not always suggest accurate data. Some of the factors that can impact the accuracy of a piece of data include:
The sensor used to measure a variable signal and convert it to a digital value will have a specified accuracy 鈥 you are converting an infinitely variable value into a discrete digital one. This accuracy factor means the digital value may vary somewhat from the original analog value.
When measuring continuous variables, inaccurate values can be collected due to issues with the sensing device. There can be a failure in the sensor 鈥 a broken wire on the input to the sensor, faulty calibration of the sensor, or an outside influence that can distort the sensor's detected value. Any of these can cause an inaccurate value to be recorded.
State, modal, and alarm signals can also report an invalid value due to common failures 鈥 a broken input or shorted wire are common fault situations.
Each piece of measured data should be individually evaluated regarding its potential impact on the software systems used to assess shop operations. If an inaccurate value is recorded, how sensitive is your system implementation to that piece of data? Remember: "Garbage in" basically guarantees "garbage out." Suppose the sensitivity to the accuracy of a specific piece of data is high. In that case, additional actions should be implemented to ensure that data is valid and accurate. Such activities can include:
Implementing a redundant sensor and comparing the values reported from both to validate that your data is accurate.
Utilizing sensor diagnostics to determine open wire, broken wire, shorted wire, temperature sensitivity, etc. Such diagnostics are often available but overlooked in many data collection processes.
Apply analytics to the data to verify that the recorded value falls within expected limits.
Providing, where possible, a calibrated reference to which the value recorded by a sensor can be periodically compared to validate accuracy.
Establish maintenance and calibration procedures to validate the integrity of the data being produced by your electronic equipment and sensors. Maintenance procedures often focus on higher-level control devices, but lower-level sensing devices should not be overlooked.
One of the biggest challenges associated with consuming measured data is that it is normally provided in its raw form 鈥 it must be interpreted to provide meaning and relevance to the manufacturing process.
Here are some typical examples of measured data as it is represented at the data source. Without additional information, it is impossible to determine what each piece of data represents.
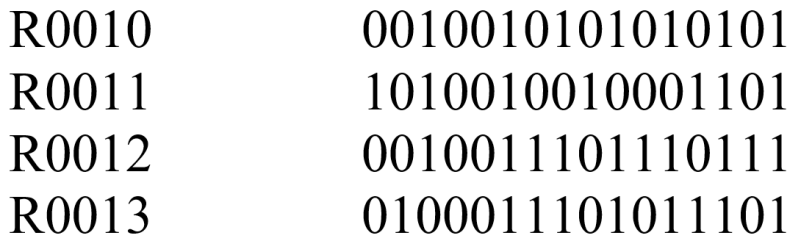
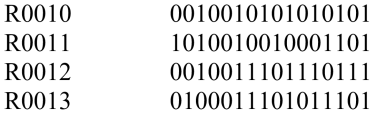
Measured data in its raw form must be transformed to make it useful for consumption. This transformation involves enhancing each piece of data by adding information about the meaning of the data (declaring a type for the data, scaling values where needed, adding units, etc.). Additionally, information must be added to establish relevance to the manufacturing process. This transformation is referred to as "adding semantics" to the data. Traditionally, this transformation is accomplished during the configuration process for each software application that uses each piece of data.
Some communications protocols pre-process data and transmit it in a more useful form. Additionally, more evolved data sources produce measured data in a form that includes some or all of the semantics from the source device. In these cases, the data is presented as either numeric or state values, which are easier to interpret than in their raw form, e.g., 357, 23.58 degrees F, on, off, auto, etc.
When semantic data is available, there are some key benefits to be gained:
Significant reduction in man-hours of effort required during the deployment of a software system 鈥 shortens deployment time.
Reduced person-hours drive lower costs.
Consistent interpretation of data across multiple sources.
Simplified maintenance of the systems consuming the data.
You can take a deeper dive and uncover more details about data and data sources for a digital manufacturing information system in AMT's digital manufacturing white paper 鈥Digital Manufacturing: Data Sources.鈥